Products & Services
商品・サービス
AIデータ分析で製造プロセスの最適化を実現!
操業データの分析で生産性効率の向上、品質改善、故障予防、人手不足解消、技術継承などの課題解決にアプローチ
操業データ分析ソリューション
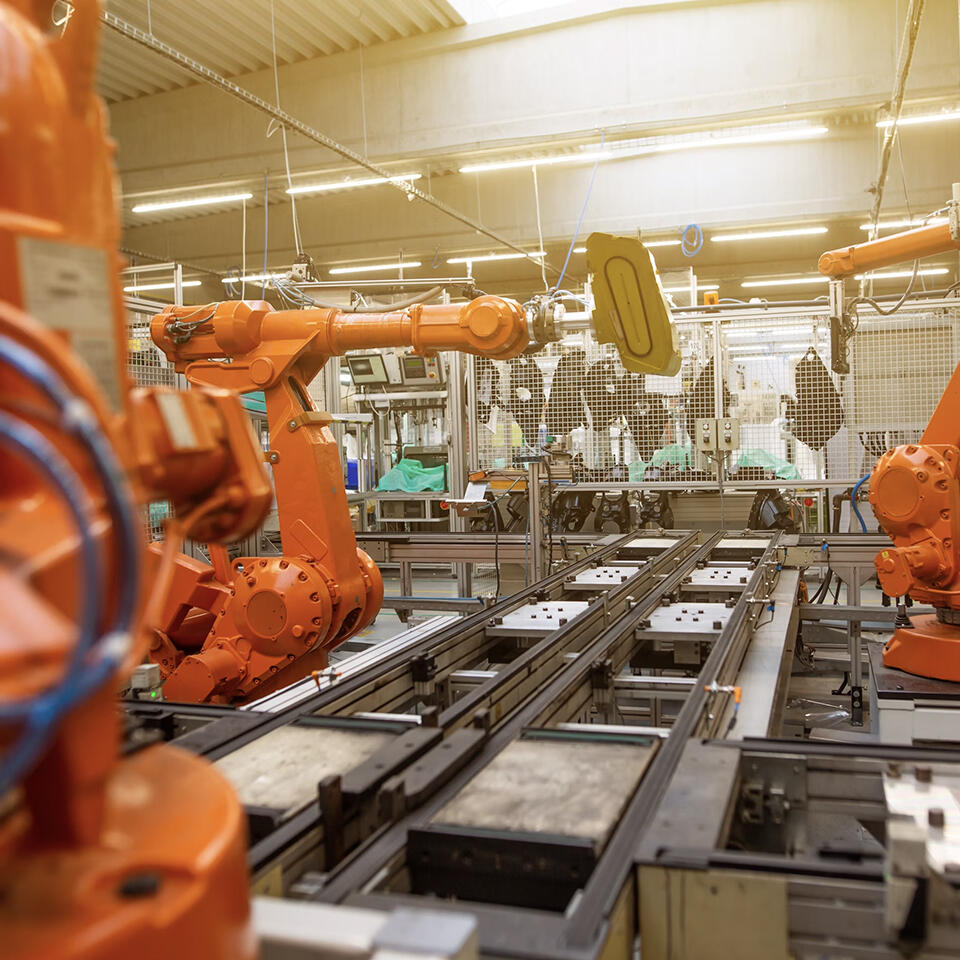
こんな課題はありませんか?
製造プロセスの作業品質に満足していますか?品質確保にお困りはありませんか?
製造プロセス(たとえば、物質の溶解処理、化学的加工や重機のリモート操縦など)において、均一の作業品質が確保できないなどの問題でお困りではありませんか?
マニュアル通りの操作を行っていても、次のようなさまざまな問題が生じる可能性があります。
物質の量が通常よりも多く溶解までに時間を要した
素材投入のタイミングが遅く材質が劣化した
負荷が掛かり過ぎて設備が故障した、加工に失敗した
操業データ、製造業データ、工場データを収集、分析して、作業品質を向上したい。
操業データとは、たとえば外気温、液温、圧力、バルブ開度、流速やライン速度、pH(ペーハー)など、時間とともに変化する計測値で構成されたデータです。製造業データ、工場データとしては、生産設備の電圧や電力、稼働データ、温度や信号、また、生産数や不良品数などが挙げられます。
これら操業データ、製造業データ、工場データの分析により、製造プロセスの作業品質に関する問題を解決することが可能です。
しかしながら、これらの操業データを有効活用したいとの思いがあっても、どのようなデータの測定が適切であるかが判断できない、データを測定、保有、活用していも十分な効果が感じられないなどの問題に直面していませんか。
また、ベテラン社員のスキルや暗黙知に頼りがちで、通常は問題がなくても、故障やトラブルが発生すると原因特定までに時間を要するなども見逃せない問題ですが大丈夫でしょうか。
NTT-ATでは長年培ったAI、データ分析スキルを活用して、操業データ、製造業データ、工場データの分析を行い、これらの問題点を解決いたします。
解決のためには
AIデータ分析により製造プロセスを見える化し、問題点をあぶり出して作業を効率化し、品質管理業務を改善します。
製造プロセスをヒアリングさせていただき、操業データを用いてAIデータ分析を行い、製造プロセスを見える化します。これにより、標準作業(最良の方法)や熟練者作業との乖離に気づきを得て、手戻りや問題の回避、ひいては作業効率化や品質向上を支援します。また、「労働人口減少に伴う人手不足」、「技術継承問題」の解決にも寄与します。
さらに、分析結果に基づいてシステム化を行うことで品質管理業務を改善いたします。お客さまのご要望に応じて、故障検知、異常検知についても対応いたします。
この商品・サービスのメリット
1 操業を把握して運用を効率化、作業品質を改善
操業データを見える化し、リアルタイムに状態を表示することで、視覚的に標準作業との乖離が分かります。
気づきを得て、問題の早期発見・対応が実施でき、問題に起因する影響を抑えます。生産ラインのボトルネックや無駄な待ち時間、生産過程の改善点を発見し、生産効率を向上
担当者毎の操業データの差から品質への影響の分析・改善
標準作業からの乖離の早期検出・リードタイムの確保
担当者の意識の喚起、行動変容の促進
2 日常の品質管理業務の改善
システム化を行うことでお客さま自身で次のような品質管理業務を目指すことが可能となります。
データ収集とモニタリング: 各種センサーや計測機器からのデータを収集、保存します。
データ見える化と洞察: データを見える化し、ボトルネックや効率化の機会を発見し、改善策の提案が可能になります。
レポート作成とコミュニケーション: 分析結果を定期的にレポートし、意思決定のサポートが可能になります。
3 属人化の解消による作業バラツキの改善
業務に関する熟練者がいれば業務はスムーズですが、一方で以下のようなリスクがあります。
担当者の不在や能力の制約が深刻な影響を及ぼす可能性があります。
業務の質が個人に依存しているため、担当者が変わるたびに変動して安定しない。
引継ぎ時にかかる時間や手間が増え、引継ぎ漏れが発生しやすくなる。
見える化を行うことにより、データに基づく対応となるため、個人差による変動が少なく業務水準を一定に保ち、かつ意思決定を早めることが可能となります。また、熟練者などからのスムーズな技術継承にも寄与いたします。
選ばれる理由
30年を超える豊富な経験・実績と深い知識
NTT-ATのデータ分析チームは、30年を超えるAIデータ分析支援実績に裏付けされた確たる技術で新たなビジネス作りを支援しております。さまざまな領域のお客さまの業務、ビジネスに対応した経験があり、AIデータ分析、モデリング、システム化、導入・運用まで、全てのプロセスにおいて価値あるソリューションを提供しております。(参考:ATデータ分析コンサルティングサービス)
商品・サービス内容
お客さまの視点で業務ヒアリング、AIデータ分析を効果的に進めていきます。
操業データを明確化してデータ分析を行います。これを効果的なものにするため、まず、お客さまの視点で十分にヒアリングを実施いたします。ヒアリング内容からお客さまの業界に対する知識を獲得し、要求事項の確認、品質指標、プロセスや課題、見える化項目の検討を行います。
次に、データと課題の関係性を把握し、必要データを明確化してAIデータ分析を行います。
これらを遂行するため、定例打合せの実施などにより、お客さまの意図を十分に反映した施策として効果的に進めていきます。
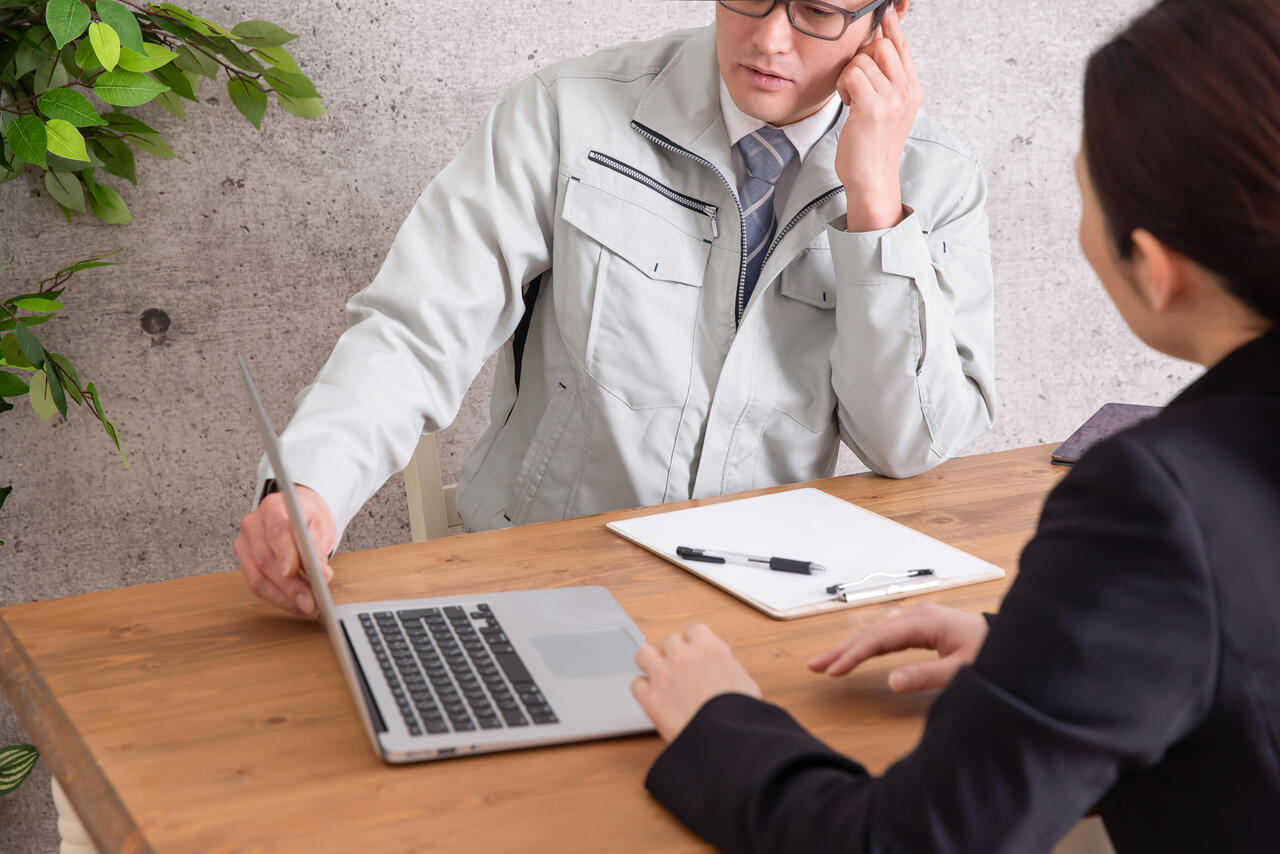
お客さまが運用可能な支援システムを提供いたします。これにより、データ分析の結果をベースとした業務が可能です。
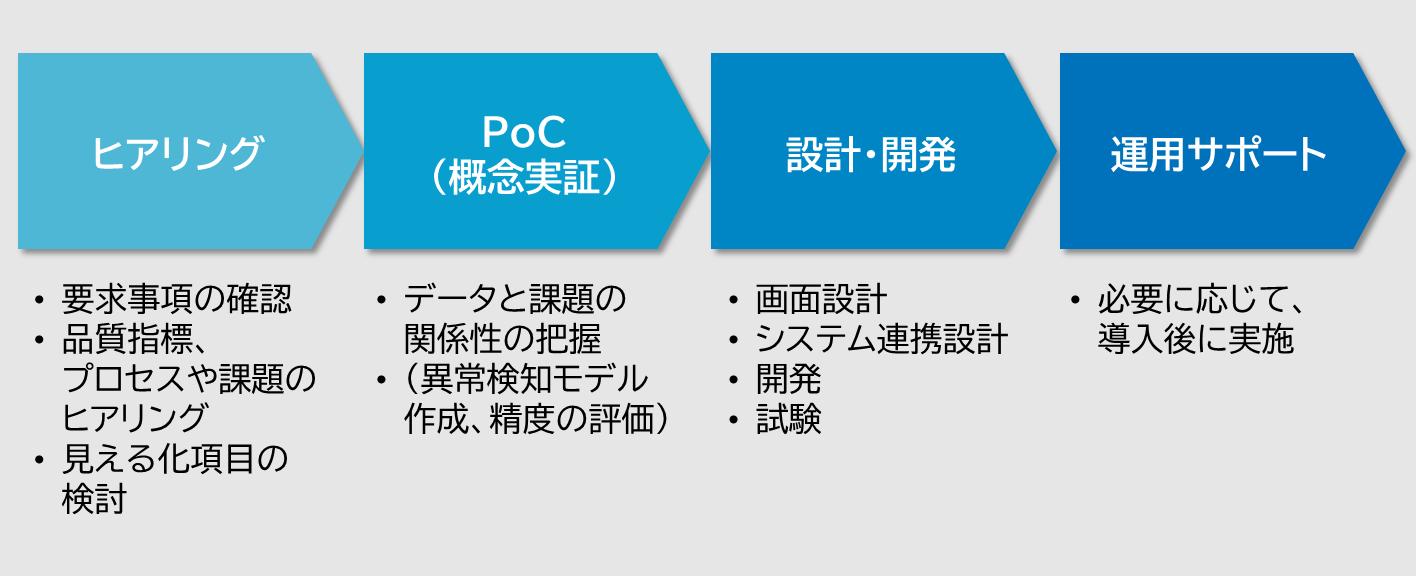
操業データ分析ソリューション導入の基本的な流れは、図の通りとなります。
ヒアリング 前述のとおり、お客様の視点で十分なヒアリングをいたします。
PoC(Proof of Concept、概念実証) ヒアリングに基づいてデータと課題の関係性を把握し、これを表現するモデルを作成してデータ分析によりモデルを評価します。必要に応じて、データと異常の関係を表す異常検知モデルを作成し、データ分析によりモデルの精度を評価します。データ分析の結果に基づいた業務の円滑な実施をご所望の場合は、さらに次の工程を行い、お客さま自身が運用可能な支援システムを実現します。
設計・開発 データ分析において効果のあった分析手法、モデルを選択し、お客様が運用可能なシステムとしてBIツールを用いて、お客さまが要望される形でデータを見える化(ダッシュボードを作成)し、お客さま自身が運用可能な価値あるシステムとしてご提供いたします。システム化を行うことでお客さま自身で本施策に基づいた品質管理業務を実施することが可能となります。
運用サポート お客さまのご要望に応じて見える化システムの運用をサポートいたします。
操業データ分析による故障検知、異常検知が可能です。
お客さまの御希望に合わせて、故障検知、異常検知の機能をご提供します。
これまでに発生した故障発生時、異常時の操業データの分析を行い、異常と各装置・設備の因果関係を明らかにします。その上で故障検知、異常検知もしくは予兆検知モデルを作成し、精度検証を行い、異常検知の仕組みを明らかにします。その後、システム化などお客さまのご要望に応じてカスタマイズいたします。
価格プラン
価格については、お問合せください。
・システム開発(ヒアリング~PoC(概念実証)~設計・開発):システム規模や画面数に応じて個別見積り
・導入後サービス:維持管理、画面追加などお気軽にご相談ください
こんな方に最適です!
製造業: 自動車、電子機器、消費財、食品・飲料などの製造業界では、生産プロセスの監視、効率化、品質管理が重要です。操業データの分析により、生産ラインの最適化や不良品の削減、メンテナンスの最適化を目ざします。
化学業: 化学プロセスの管理と制御において、温度、圧力、流量、化学組成などのデータを分析することで、製品品質の向上や生産性の最大化が図られます。
エネルギー業: 発電所や原油精製などのエネルギー関連施設では、温度、圧力、流量、エネルギー消費などのデータを分析して、効率化とコスト削減を目ざします。
鉱業: 採掘や精錬プロセスにおいて、地質データ、機械の稼働データ、原材料の特性などを分析し、生産性の向上と安全性の確保を目ざします。
食品加工業: 食品の製造や加工プロセスにおいて、温度管理、流量、pH、残留物の検査結果などのデータを分析して、品質管理と安全性の確保を行います。
導入イメージ
導入例1 操業データ分析による品質向上
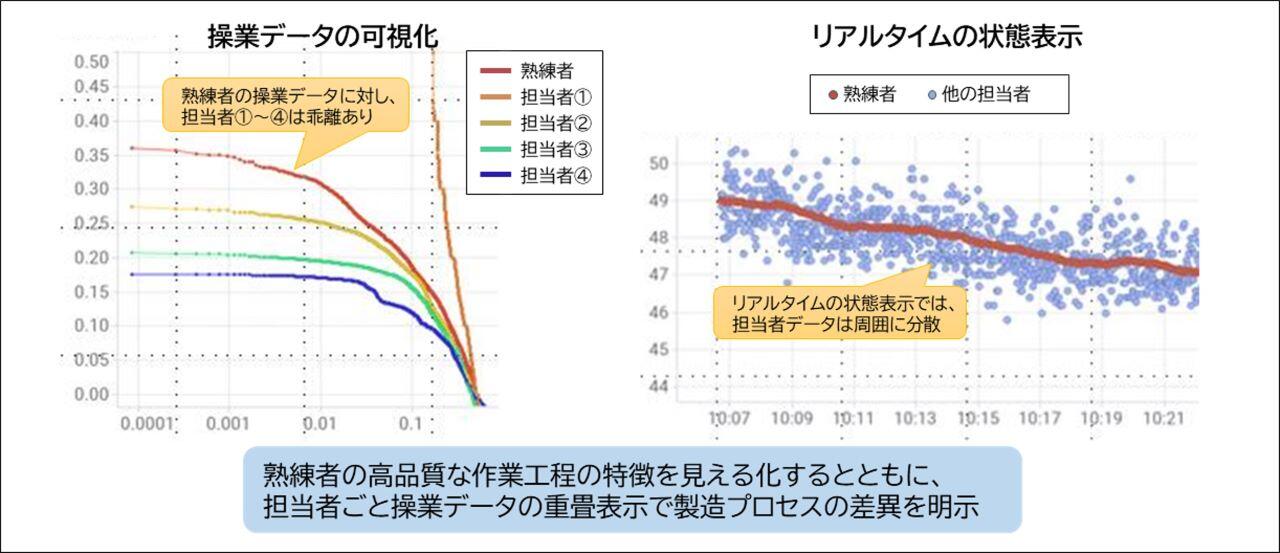
製造プロセスや業務手順の標準化を行っても、作業員によっては品質にばらつきが生じる場合があり、生産コストの増加、利益の圧迫につながります。
当ソリューションでは、担当者毎に各工程での操業データの可視化・分析を行い、熟練者の高品質な作業工程の特徴を明らかにし、熟練者と担当者との作業工程の差を明示することで品質の向上に貢献いたします。
次のような効果が期待できます。
熟練者ノウハウ共有: 言葉では表現が難しい熟練者の作業工程をデジタル化
作業員の品質均一化: 品質の一貫性の向上/ばらつきの減少
製造コスト削減: 手戻りの削減、不良品発生率の減少、再加工の削減
競争力向上 : 高品質な製品を提供することで競争力強化
可視化には、BIツールであるTIBCO Spotfire®を使用しています。
導入例2 操業データ分析による異常検知
製造業では、装置や設備の異常(故障など)は製造ラインの停止や歩留まり低下などを引き起こすため、いかに稼働率を上げるかがビジネス成功への鍵となります。
当ソリューションでは、これまでに発生した異常時の操業データの分析を行い、異常と各装置・設備の因果関係を明らかにします。その上で異常検知もしくは予兆検知モデルを作成し、精度検証を行います。その後、システム化などお客さまのご要望に応じてカスタマイズいたします。
次のような効果が期待されます。
稼働率の向上: 製造ラインの停止や生産の中断を最小限に抑えることでの生産量や効率の向上
歩留まりの向上: 異常の早期検知によって、不良品の発生を減少
運用コスト削減: 異常が発生した際の生産中断のコストを削減、メンテナンスの最適化
データ駆動の最適化: 装置や設備の動作パターンを把握し、最適な運用条件やメンテナンスを実施
お問い合わせ
現状の課題、お悩みをお聞かせください。
製造プロセス生産性のお悩みに関する課題をお聞かせください。
NTT-ATのソリューションがお役に立てるかどうか、ご相談させてください。
よくあるご質問
どれくらいの期間を要しますか
課題の難易度、データの種類や量によって変わりますが、おおよそ、ヒアリング、要件の明確化、PoCに3か月程度かかります。
またシステム開発の設計・開発フェーズについては規模にもよりますが、最低3か月程度を想定しています。
どのくらいの費用となりますか
期間と同様、課題の難易度、データの種類や量によって変わりますので、個別にお問い合わせください。
お問い合わせ、事前ヒアリングについては無償で対応いたします。